
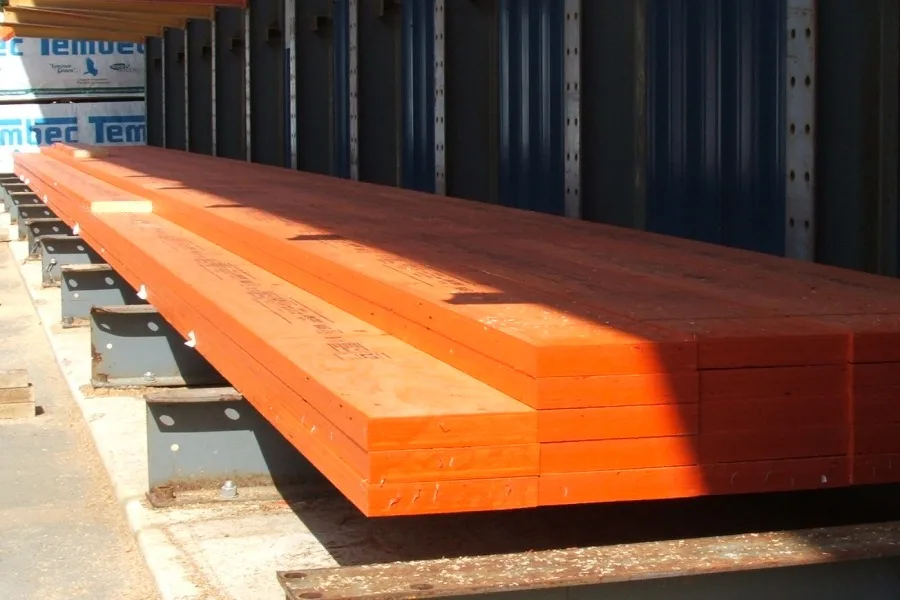
LVL is a highly versatile wood-based product.It is the strongest wood-based material relative to its density.It is also stronger in relation to its weight. LVL has an excellent size-to-strength and weight-to-strength ratio, i.e., a smaller sized LVL possesses greater strength than solid lumber.The length, depth, and strength of LVL beams effectively carry loads over long spans. As veneers in LVL are oriented in the same direction, they are particularly suitable for beam construction.The rate varies based on the timber species used and the size of the member. The fire resistance of LVL is similar to that of solid timber, with a slow and predictable charring rate.
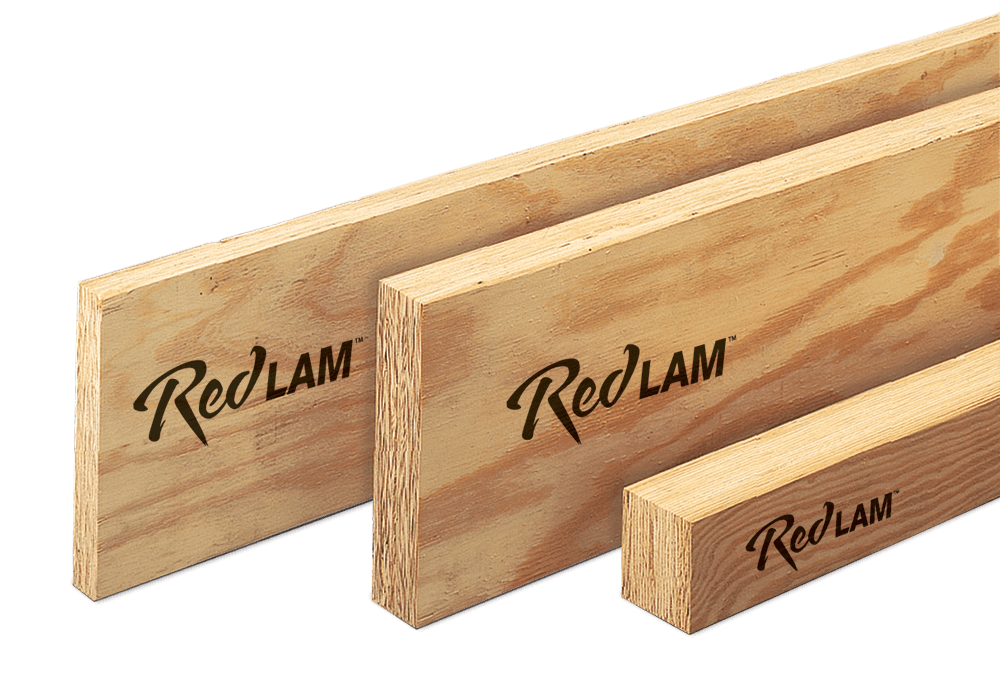
Sheets or billets of LVL are manufactured to a thickness of 35 to 63 mm and lengths up to 12 m.Holes can also be made on these members for the installation of services. LVL can be sawn, nailed, and drilled using normal tools.Hence, LVL should be treated with preservatives to protect against decay or infestation for such applications. LVL is prone to decay when exposed to high moisture content or when used in an unventilated area.These veneers are well treated, scanned for defects, analyzed for moisture content, and clipped using a rotary clipper to a width equal to 1.4 m for LVL production. The veneers used for manufacturing of LVL have a thickness of less than 3 mm and are produced using a rotary peeling technique.The veneers are stacked in the same direction, i.e., the wood grain is perpendicular to the length of the billet (a billet is a complete board formed by stacking them). The veneers are layered and bonded together with a moisture-resistant adhesive.LVL comes under the category of structural composite lumber (SCL) and is made of dried and graded wood veneers, strands, or flakes.Features of Laminated Veneer Lumber (LVL)įeatures of Laminated Veneer Lumber (LVL).Other times the panels are shipped to our shop for further fitting of steel connections to speed up site erection. Machining and milling of holes is sometimes performed at the producers plant based on our carefully detailed fabrication drawings and CNC machine files, and the product is shipped straight to site. We procure LVL from a North American producer and can meet the volume and quality requirements of any job. Our LVL Fabrication and Procurement Process In so-called 'Q' and 'T' lay-ups, some veneers are laid so that their grain is contrary to the grain direction most of the veneers, giving rigidity to the LVL so it does not warp and twist. In typical manufacture, all veneers are laid up so the grain direction is the same in all veneers. Scarf joints (chamfer cuts) create joints between sections of veneers. The LVL manufacturing process of veneering and gluing enables large members to be made from smaller trees, creating efficient utilisation of wood fibre.
Lvl lumber full#
With increasing interest in mass timber use for diaphragm applications (floors, roofs, walls), manufacturers are beginning to position LVL in full sheet format, and some interesting configurations involve laminating LVL beams side-to-side to make thin, solid panels - exposing the veneer end grain instead of the face grain.
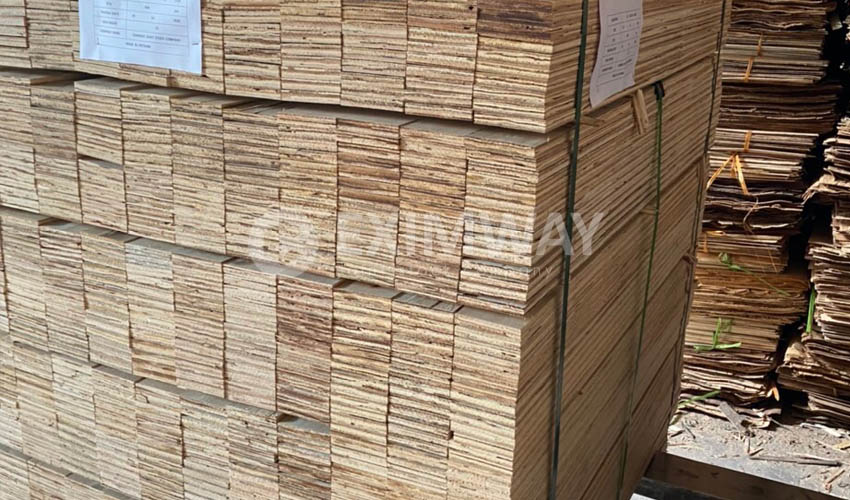
Engineered to precise design values and with a very high strength-to-weight ratio, LVL panels are suitable for structural wall, floor and roof applications. Vertically laminated veneer lumber (LVL) panels are made from “peeler logs" in the same production lines as LVL beams.
